As companies transition from human workers to robots performing tasks in the workplace, OSHA is keeping its eye on potential safety issues. The growing influence of artificial intelligence in the workplace necessitates comprehensive safety regulations to address new challenges. Additionally, advancements in robotics technology are enhancing workplace safety across various industries by automating hazardous tasks and reducing risks.
Companies that don’t have comprehensive safety plans related to working with robots could be at risk of receiving OSHA citations. Although current regulations may be 15 years old or older, the organization believes that they provide an adequate regulatory framework for employers to follow.
To reduce the risk of workplace injuries in areas occupied by robots, walls, and gates should be erected around such machines. This will prevent human workers from entering robot work areas where they could be hurt by moving parts. While caution tape or other floor markings may decrease the risk of injury, they are not sufficient to keep workers free from harm. Ideally, an employer will install a presence-sensing device that will slow or stop the robot when a human is nearby.
Employee training programs and a company safety policy can reduce the risk of employees getting hurt while on the job. Both new employees and experienced workers should receive training whenever necessary to keep them up-to-date about the equipment that they are working with. New hires should not be allowed to work with machines on their own until they can do so in a safe and responsible manner.
Those who are hurt in a workplace accident may wish to talk to an attorney regarding their injuries. It may be possible to receive workers’ compensation benefits that may pay for medical treatment and long-term care expenses. They may also include a percentage of wages lost during the recovery period. Many claimants find the assistance of an attorney to be helpful at all stages of the process.
Introduction
The increasing use of robots in various industries has transformed the way we work, making tasks more efficient and precise. However, this shift also raises concerns about workplace safety and the potential risks associated with robotic systems. As robots become more common in the workplace, it is essential to address safety concerns and ensure that workers are protected from potential hazards. In this article, we will explore the impact of robots on occupational safety, discuss ways to ensure worker safety with robots and examine OSHA regulations and compliance.
The Impact of Robots on Occupational Safety
Robots have the potential to significantly improve occupational safety by automating repetitive tasks, reducing the risk of workplace injuries, and enhancing precision and accuracy. According to the Bureau of Labor Statistics, there were approximately 2.8 million nonfatal workplace injuries and illnesses in 2022 in the United States alone. By automating hazardous tasks, robots can reduce the risk of accidents for human workers. Additionally, robots can perform tasks that are physically demanding or require working in hazardous environments, reducing the risk of injuries and illnesses.
Ensuring Worker Safety with Robots
Ensuring worker safety with robots requires a comprehensive approach that includes proper training, regular maintenance, and adherence to safety protocols. Employers must provide thorough training on the safe use of robotic systems, including how to operate, maintain, and troubleshoot the equipment. Regular maintenance is also crucial to prevent mechanical failures and ensure that the robots are functioning correctly. Furthermore, employers must implement comprehensive safety protocols, including emergency response plans and procedures for reporting incidents.
OSHA Regulations and Compliance
The Occupational Safety and Health Administration (OSHA) plays a crucial role in regulating workplace safety in the age of automation. OSHA sets and enforces standards to ensure safe and healthful working conditions across various industries. As automation becomes more widespread, OSHA is proactively updating its guidelines to address the specific challenges posed by automated systems. Employers must comply with OSHA regulations, including providing proper training, maintaining equipment, and implementing safety protocols. Failure to comply with OSHA regulations can result in citations and fines.
Education and Outreach for Safe Robot Use
Education and outreach are essential for promoting safe robot use and ensuring that workers are aware of the potential risks and benefits associated with robotic systems. Employers must provide ongoing training and education on the safe use of robots, including how to operate, maintain, and troubleshoot the equipment. Additionally, employers must promote a culture of safety, encouraging workers to report incidents and near-misses. By educating workers on the safe use of robots, employers can reduce the risk of workplace injuries and ensure a safe and healthy work environment.
Why Rubin, Glickman, Steinberg & Gifford P.C. Is Your Advocate for Workplace Safety and Workers’ Compensation
The rapid integration of robotics and automation in the workplace brings both opportunities and challenges, especially in maintaining worker safety. At Rubin, Glickman, Steinberg & Gifford P.C., we have over 65 years of experience helping injured workers navigate workers’ compensation claims and holding employers accountable for safety violations. Our team is dedicated to protecting your rights and ensuring you receive the compensation and support you deserve.
Recognized by U.S. News & World Report and Pennsylvania Super Lawyers, we provide thorough representation, whether your case involves traditional workplace hazards or injuries related to automated systems. Contact us at (215) 822-7575 or through our contact form to discuss your legal options and safeguard your future.
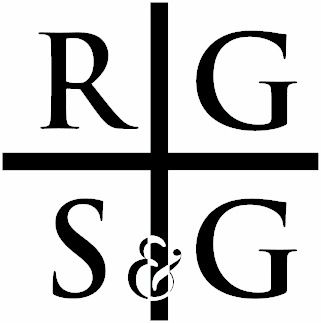
Rubin, Glickman, Steinberg & Gifford P.C.
Pennsylvania Attorney's
January 29, 2025